Outsert techniek
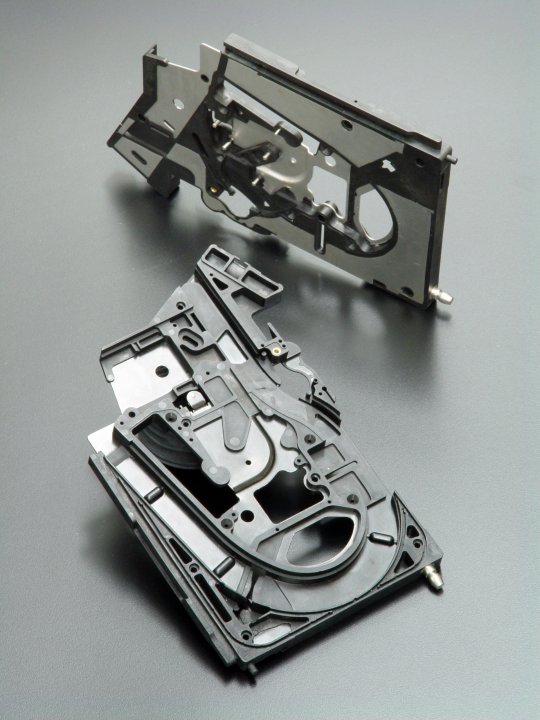
Outsert techniek. Stijfheid van metaal – vormvrijheid van kunststof.
Wij combineren het montage spuitgieten met de hybride technologie en produceren hoog integratieve onderdelen. Rationeel in één spuitgietcyclus.
Belangrijkste toepassing is de fijnmechanische module. In het spuitgieten assembleren wij beweeglijke en onbeweeglijke functionele elementen van kunststof op gestanste of gesneden metalen printplaten. De functionaliteit bepaalt de constructie van de pasvorm.
Gefixeerde montage. Een stevig bevestigt basisonderdeel zit of vastgemaakt door een rond gestanste opening met draaizekering of het zit vastgemaakt in een aslager. Typische functies zijn aanslagen, opnames, verstijvingselementen, inserts, glijlagers, veerelementen, fixeerringen, doorvoeringen, consoles, snaphaken en nokken.
Draaibaar gemonteerd onderdeel. Een basisonderdeel in een rond gestanste opening is draaibaar. Typische functies zijn draaiknoppen, hefbomen, nokkenschijven, actuatoren en tandwielen.
Beweegbaar gemonteerd onderdeel. Een basisonderdeel in een recht of gebogen constante sleuf kan beweegbaar zijn. Typische functies zijn glijblokken, pallen of vergrendelingen.
Naar behoefte worden stansdelen, persdelen en buigdelen van verschillende grondstoffen als printplaat verwerkt. Typische print grondstoffen zijn aluminium, CFK, koper, messing of staal. Innovatieve modules ontstaan door uitbreiding met het meer componenten spuitgieten of inserttechniek.